In this tutorial article you will learn how a stepper motor works. We will cover the basic working principles of stepper motors, their driving modes and the steppers types by construction. You can watch the following video or read the written article.
Working Principle
Stepper motor is a brushless DC motor that rotates in steps. This is very useful because it can be precisely positioned without any feedback sensor, which represents an open-loop controller. The stepper motor consists of a rotor that is generally a permanent magnet and it is surrounded by the windings of the stator. As we activate the windings step by step in a particular order and let a current flow through them they will magnetize the stator and make electromagnetic poles respectively that will cause propulsion to the motor. So that’ the basic working principle of the stepper motors.
Driving Modes
There are several different ways of driving the stepper motor. The first one is the Wave Drive or Single-Coil Excitation. In this mode we active just one coil at a time which means that for this example of motor with 4 coils, the rotor will make full cycle in 4 steps.
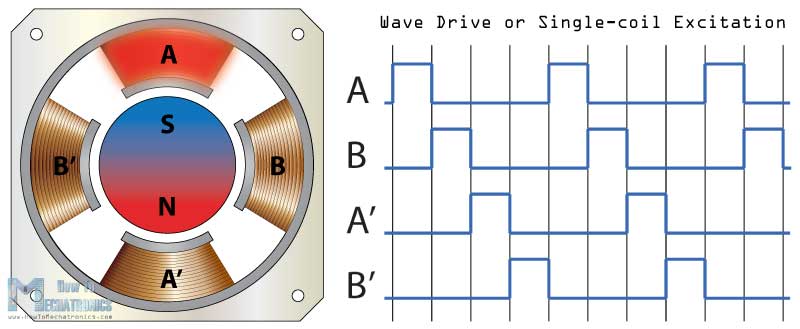
Next is the Full step drive mode which provides much higher torque output because we always have 2 active coils at a given time. However this doesn’t improve the resolution of the stepper and again the rotor will make a full cycle in 4 steps.
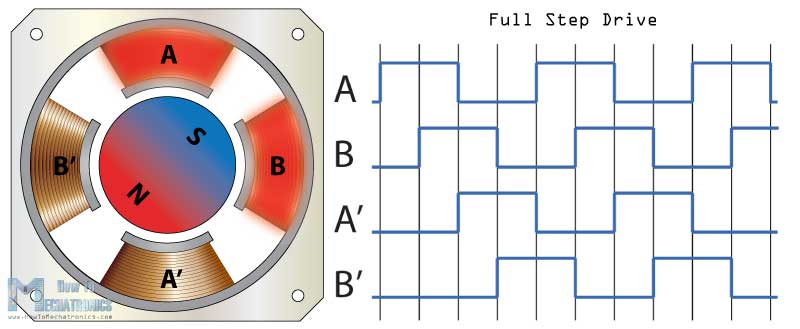
For increasing the resolution of the stepper we use the Half Step Drive mode. This mode is actually a combination of the previous two modes.
Here we have one active coil followed by 2 active coils and then again one active coil followed by 2 active coils and so on. So with this mode we get double the resolution with the same construction. Now the rotor will make full cycle in 8 steps.
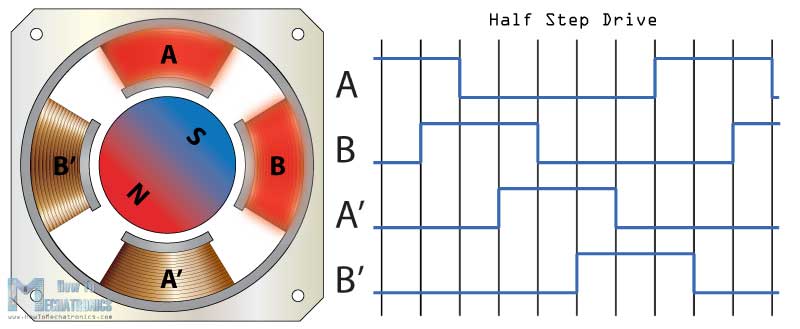
However the most common method of controlling stepper motors nowadays is the Microstepping. In this mode we provide variable controlled current to the coils in form of sin wave. This will provide smooth motion of the rotor, decrease the stress of the parts and increase the accuracy of the stepper motor.
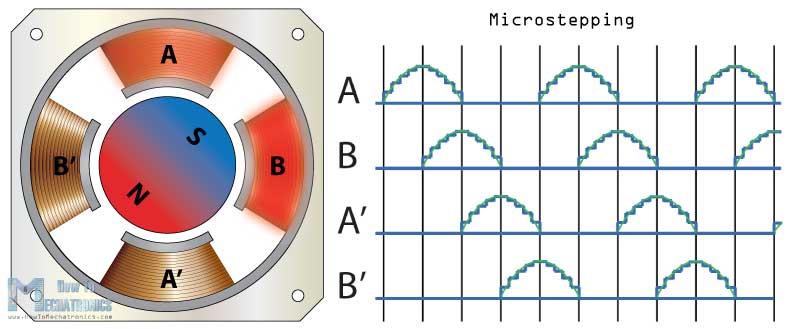
Another way of increasing the resolution of the stepper motor is by increasing the numbers of the poles of the rotor and the numbers of the pole of the stator.
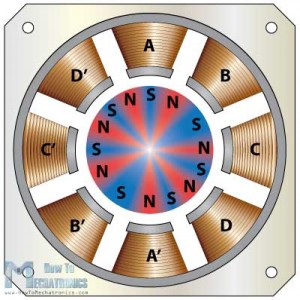
Stepper Motor Types by Construction
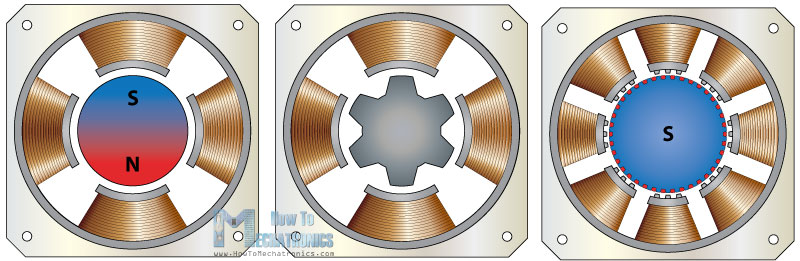
By construction there are 3 different types of stepper motors: permanent magnet stepper, variable reluctance stepper and hybrid synchronous stepper motor.
The Permanent Magnet stepper has a permanent magnet rotor which is driven by the stators windings. They create opposite polarity poles compared to the poles of the rotor which propels the rotor.
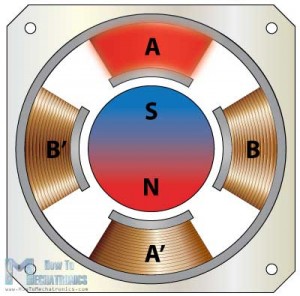
The next type, the Variable Reluctant stepper motor uses a non-magnetizes soft iron rotor. The rotor has teeth that are offset from the stator and as we active the windings in a particular order the rotor moves respectively so that it has minimum gab between the stator and the teeth of the rotor
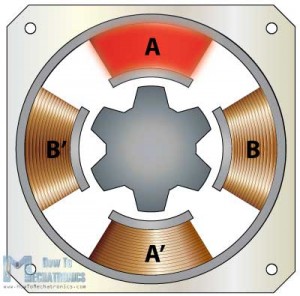
The Hybrid Synchronous motor is combinations of the previous two steppers. It has permanent magnet toothed rotor and also a toothed stator. The rotor has two sections, which are opposite in polarity and their teeth are offset as shown here.
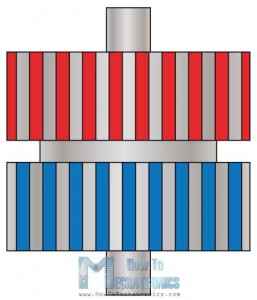
This is a front view of a commonly used hybrid stepper motor which has 8 poles on the stator that are activated by 2 windings, A and B. So if we activate the winding A, we will magnetize 4 poles of which two of them will have South polarity and two of them North polarity.
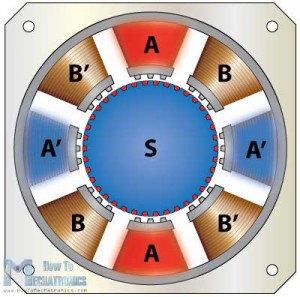
We can see that in such a way the rotors teeth are aligned with the teeth of poles A and unaligned with the teeth of the poles B. That means that in the next step when we turn off the A poles and activate the B poles, the rotor will move counter clock wise and its teeth will align with the teeth of the B poles.
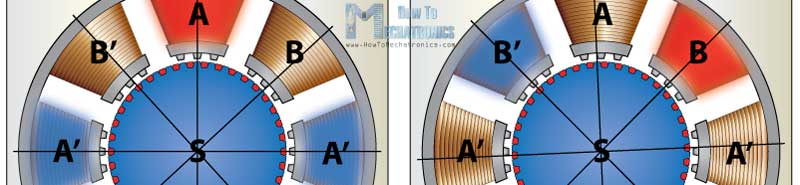
If we keep activating the poles in a particular order the rotor will move continuously. Here we can also use different driving modes like the wave drive, full step drive, half step drive and microstepping for even further increasing the resolution of the stepper motor.